The aerospace sector is transforming. As manufacturers face unprecedented production rates while preparing for the next generation of aircraft, supply chains are being stretched, traditional manufacturing methods are being tested and pressure is mounting to deliver parts faster without compromising quality, cost or sustainability.
This challenge is especially pronounced in the production of complex aerostructures and composite tooling. Once lengthy and linear processes, these workflows now face flexibility, scalability and near-immediate responsiveness demands. While many suppliers grapple with long lead times, skill shortages and supplier fragility, ST Engineering MRAS is actively reshaping the model.
With its Quick Turn Tooling capability, built on in-house additive manufacturing and digital integration, MRAS offers a faster, more resilient and more sustainable path to composite tooling. It is a model that aligns with the industry’s future trajectory.
Disrupting the Traditional Tooling Model
Historically, aerospace tooling development has relied on CNC-machined metal or composite molds. These conventional methods require extensive planning, expert programming and skilled operation. Each step adds time, cost and potential delay. Furthermore, they often restrict the number of design iterations a team can afford, forcing compromises on part optimization.
ST Engineering MRAS has replaced this linear and resource-heavy process with a faster and more flexible alternative using Fused Deposition Modeling (FDM). This additive manufacturing method constructs tooling layer by layer using thermoplastic materials, eliminating the need for complex setups or outsourcing.
The benefits are immediate. FDM tooling can be created at a fraction of the time and at around 25% lower cost than traditional counterparts. Design changes are no longer disruptive. If a revision is needed, a new tool can be printed quickly and inexpensively, supporting better engineering decisions without affecting the overall schedule.
From Design to Part in Days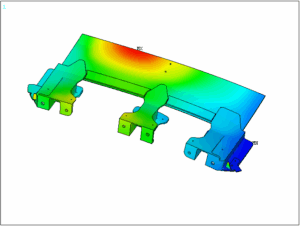
A key enabler of this speed is MRAS’s integrated digital workflow. The system level approach connects the design, simulation and manufacturing into a single data stream eliminating inefficiencies. The results are that the entire tooling and manufacturing development lifecycle is compressed into weeks or even days for certain applications.
This system removes the delays typically caused by departmental handoffs or communication gaps. Rather than waiting for a CAD file to be processed by a separate tooling team or an external supplier, MRAS engineers can design and print tooling directly. This accelerates decision-making and keeps development timelines on track.
The system also facilitates rapid iteration of tool designs, which is particularly valuable in the early stages of product development. Traditional methods follow a linear process in which launching tooling efforts follow the final product design reviews. This linear method pushes manufacturing development to the end of the cycle, and as such, the feedback loop into the product design can be long and costly. In this model, tooling and manufacturing development can be started as soon as the concept designs are completed, allowing the design and manufacturing team to trial multiple concepts and adjust designs based on test data, resulting in a product that has an optimized design and manufacturing method.
Eliminating Digital Silos
Beyond speed, the MRAS process also removes one of the most persistent inefficiencies in traditional aerospace manufacturing. Digital silos often slow projects by separating design from tooling and manufacturing.
At MRAS, digital tools and 3D printing have empowered engineers to own more of the development cycle. Designers can test tooling ideas directly, make modifications in real time and collaborate more freely with downstream stakeholders. Problem-solving becomes more agile, and overall engineering velocity increases.
This digital integration also supports better use of talent. MRAS has reduced its dependence on specialized CNC programmers and machinists by lowering the technical barrier to tooling development. Instead, the company focuses on cross-functional training and digital upskilling, helping its workforce adapt and respond quickly to evolving program needs.
Strengthening Supply Chain Stability
Supply chain fragility has emerged as a significant risk in aerospace manufacturing, with many programs suffering from late deliveries, capacity constraints and supplier financial instability. In response, MRAS has strategically shifted toward internalization, bringing key tooling operations in-house to reduce external dependencies.
This decision improves delivery reliability and gives customers greater confidence and control. With wholly owned and operated 3D printing equipment, MRAS maintains oversight of both capacity and quality, ensuring that tools are produced on time and to specification.
The additive process also reduces financial risk for customers. Tooling investment is lower, and the ability to support low-rate initial production without significant capital outlays allows MRAS’s partners to progress with greater confidence. Whether launching a new program or scaling production, they benefit from faster timelines, lower costs+ and more predictable outcomes.
Scalable for High-Rate Production
As the aerospace industry moves toward building more than 100 aircraft per month, production systems must evolve to support this volume. MRAS’s Quick Turn Tooling is designed for scalability.
The company’s approach involves producing rapid prototype tools and high-quality masters that can be reused across multiple cycles. These masters are archived and catalogued, ready to be reproduced or adapted. This provides built-in resilience for high-volume production lines.
Composite tooling itself is already proven at scale. MRAS’s innovation lies in accelerating access to that tooling, enabling OEMs and Tier 1 suppliers to move from concept to full-rate production faster than ever before.
Supporting Sustainability Through Smarter Manufacturing
Traditional tooling methods are inherently wasteful. Subtractive processes like machining remove material from large blocks, often discarding more than half the starting volume. Additive manufacturing changes that model by building only what is needed and significantly reducing scrap.
MRAS’s use of 3D printing supports the industry’s broader sustainability goals. Not only does it reduce material waste and energy use, but it also shortens the total development timeline. This minimizes the environmental footprint of each part’s lifecycle. Because the process is adaptable, design changes can be implemented without the carbon cost of retooling an entire production line.
This transition to leaner, cleaner tooling is a practical and effective step toward greener aerospace manufacturing.
Proven Value in the Field
Feedback from MRAS customers reinforces the tangible benefits of the Quick Turn Tooling model. Speed consistently ranks as the most appreciated factor. Teams gain the ability to move from request to part delivery in a matter of weeks. This responsiveness is critical for programs operating on tight schedules or facing sudden engineering changes.
It is also clear that few suppliers offer this level of capability. While additive manufacturing is widely discussed across the industry, few have adopted it at scale for composite tooling. MRAS stands out as a company that not only deploys the technology but also builds a robust and repeatable process around it.
As more customers discover what is possible with this approach, the industry standard is beginning to shift.
A Blueprint for the Future
As aerospace manufacturing continues to evolve, companies that embrace flexibility, speed and innovation will lead the way. ST Engineering MRAS, through its Quick Turn Tooling capability, has positioned itself at the forefront of this movement.
For manufacturers seeking to reduce risk, accelerate time to market and support sustainable growth, MRAS offers more than a service –it delivers a strategic advantage. By rethinking what tooling can be, MRAS is helping the industry move forward with greater confidence and clarity.